Welding, a vital skill in numerous industries, involves fusing metal pieces together using heat. Is welding hard to learn? Absolutely. This article explores the challenges and rewards of learning to weld, providing insights for beginners and those considering this career path. LEARNS.EDU.VN offers resources and guidance to help you master this valuable trade. Discover the intricacies of welding training, essential skills, and career prospects, and find out how you can start your welding journey with confidence. Welding education and hands-on experience are key to success.
1. Understanding the Welding Landscape
Welding is the art and science of joining metals by applying heat, pressure, or both, creating a strong bond. It’s a crucial process in various industries, from construction and manufacturing to automotive and aerospace. But How Hard Is Welding To Learn?
- Definition of Welding: The process of joining two or more metal pieces by creating a strong, permanent bond.
- Importance in Various Industries: Essential for construction, manufacturing, automotive, aerospace, and more.
- Overview of Different Welding Processes: Including SMAW, GMAW, GTAW, and FCAW, each with unique applications.
2. Initial Hurdles in Learning Welding
The initial stages of learning to weld can be daunting. Mastering the fundamentals requires dedication and patience.
- Coordination and Motor Skills: Developing the hand-eye coordination needed for precise welding.
- Understanding Safety Protocols: Learning and adhering to strict safety measures to prevent accidents.
- Familiarization with Equipment: Understanding the various tools and machines used in welding.
- Material Preparation: Properly preparing materials for welding, including cleaning and aligning.
- Setup and Calibration: Setting up the welding equipment correctly for different types of metals and welding processes.
3. Key Welding Techniques and Their Difficulty Levels
Different welding techniques have varying levels of difficulty, each requiring specific skills and knowledge.
3.1. Shielded Metal Arc Welding (SMAW) – Stick Welding
SMAW, also known as stick welding, is one of the most versatile and widely used welding processes.
- Process Description: Using a covered electrode to create an arc between the electrode and the base metal.
- Difficulty Level: Moderate to high due to manual arc control and slag removal.
- Applications: Construction, repair work, and outdoor welding.
- Skills Required: Consistent arc length, proper travel speed, and slag removal techniques.
- Advantages: Portability and suitability for various metals.
- Disadvantages: Lower deposition rate and requires frequent electrode changes.
3.2. Gas Metal Arc Welding (GMAW) – MIG Welding
GMAW, commonly known as MIG welding, is popular for its ease of use and efficiency.
- Process Description: Using a continuously fed wire electrode and a shielding gas to protect the weld area.
- Difficulty Level: Low to moderate, making it a good starting point for beginners.
- Applications: Manufacturing, automotive repairs, and general fabrication.
- Skills Required: Consistent travel speed, maintaining a proper standoff distance, and adjusting wire feed speed.
- Advantages: High deposition rate, clean welds, and easy to learn.
- Disadvantages: Less portable than SMAW and not suitable for outdoor welding without wind protection.
3.3. Gas Tungsten Arc Welding (GTAW) – TIG Welding
GTAW, or TIG welding, is known for producing high-quality, precise welds.
- Process Description: Using a non-consumable tungsten electrode to create an arc, with a separate filler metal if needed.
- Difficulty Level: High, requiring excellent hand-eye coordination and precise control.
- Applications: Aerospace, automotive, and high-precision welding.
- Skills Required: Precise torch control, filler metal feeding, and maintaining consistent arc length.
- Advantages: High-quality welds, suitable for a wide range of metals, and precise control.
- Disadvantages: Slower welding speed and requires a high level of skill.
3.4. Flux-Cored Arc Welding (FCAW)
FCAW is similar to MIG welding but uses a flux-cored electrode, making it suitable for outdoor applications.
- Process Description: Using a continuously fed tubular electrode filled with flux, which provides shielding without external gas.
- Difficulty Level: Moderate, offering a balance between ease of use and weld quality.
- Applications: Construction, heavy fabrication, and outdoor welding.
- Skills Required: Maintaining consistent travel speed, adjusting voltage and wire feed speed, and understanding flux types.
- Advantages: High deposition rate and suitable for dirty or rusty metals.
- Disadvantages: Produces slag, which must be removed after welding.
Welding Process | Description | Difficulty Level | Applications | Skills Required |
---|---|---|---|---|
SMAW (Stick) | Covered electrode creates an arc. | Moderate to High | Construction, repair, outdoor welding | Arc control, travel speed, slag removal |
GMAW (MIG) | Continuous wire electrode and shielding gas. | Low to Moderate | Manufacturing, automotive repairs, general fabrication | Consistent speed, standoff distance, wire feed adjustment |
GTAW (TIG) | Non-consumable tungsten electrode, separate filler metal. | High | Aerospace, automotive, high-precision welding | Torch control, filler metal feeding, arc length |
FCAW | Tubular electrode filled with flux, no external gas needed. | Moderate | Construction, heavy fabrication, outdoor welding | Consistent speed, voltage adjustment, understanding flux types |
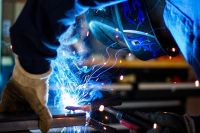
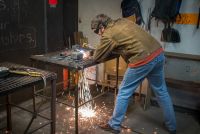
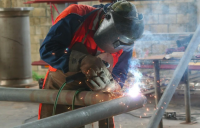
4. Essential Skills Beyond Technique
Welding is not just about mastering techniques; it also requires a range of other essential skills.
- Blueprint Reading: Interpreting technical drawings and understanding welding symbols.
- Metallurgy Basics: Understanding the properties of different metals and their welding characteristics.
- Problem-Solving: Diagnosing and resolving welding issues and defects.
- Mathematics: Applying basic math skills for measurements and calculations.
- Communication: Effectively communicating with team members and supervisors.
5. Common Challenges and How to Overcome Them
Learning to weld comes with its share of challenges, but with the right approach, these can be overcome.
- Arc Control Issues: Maintaining a stable arc can be challenging, especially for beginners. Practice and proper machine settings are key.
- Weld Defects: Porosity, undercut, and cracking are common defects. Understanding their causes and prevention methods is crucial.
- Material Distortion: Heat can cause materials to warp or distort. Proper welding sequences and heat control can minimize this.
- Slag Inclusion: Slag trapped in the weld can weaken it. Thorough cleaning between passes is essential.
- Burn Through: Welding too hot or too slow can cause burn-through. Adjusting settings and travel speed can prevent this.
- Lack of Fusion: Insufficient heat can lead to a weak bond. Ensuring proper heat input and joint preparation is vital.
6. The Role of Formal Training and Education
Formal training and education play a crucial role in developing competent welders.
- Vocational Schools: Offering comprehensive welding programs with hands-on training.
- Community Colleges: Providing associate degrees and certificate programs in welding technology.
- Apprenticeships: Combining on-the-job training with classroom instruction.
- Online Courses: Offering flexibility for those who cannot attend traditional classes.
7. Benefits of Professional Certification
Professional certifications validate your skills and enhance your career prospects.
- American Welding Society (AWS): Offering certifications for various welding processes and specialties.
- Certified Welding Inspector (CWI): Ensuring welds meet industry standards.
- Certified Welding Educator (CWE): Validating expertise in welding instruction.
- Increased Job Opportunities: Certified welders are in high demand across industries.
- Higher Earning Potential: Certification often leads to better pay and career advancement.
8. Is Welding a Good Career Choice?
Welding offers a stable and rewarding career path with numerous opportunities for growth.
- Job Market Outlook: High demand for skilled welders in various industries.
- Earning Potential: Experienced welders can earn competitive salaries.
- Career Advancement: Opportunities to specialize in areas like underwater welding, pipe welding, and robotic welding.
- Job Satisfaction: The satisfaction of creating and repairing structures with your own hands.
- Entrepreneurial Opportunities: Starting your own welding business.
9. Career Paths in Welding
Welding offers a diverse range of career paths, each with its own set of challenges and rewards.
- Structural Welder: Constructing and repairing buildings, bridges, and other structures.
- Pipe Welder: Welding pipes for oil, gas, and water distribution systems.
- Automotive Welder: Working on car frames, exhaust systems, and other automotive components.
- Aerospace Welder: Welding aircraft components using specialized techniques.
- Underwater Welder: Performing welding repairs and construction underwater.
- Robotic Welder: Operating and maintaining automated welding systems.
- Welding Inspector: Ensuring welds meet quality standards and safety regulations.
- Welding Engineer: Designing welding procedures and processes.
- Welding Instructor: Teaching welding techniques to aspiring welders.
10. Essential Tools and Equipment
Having the right tools and equipment is crucial for successful welding.
- Welding Machine: The heart of the welding setup, providing the necessary power.
- Welding Helmet: Protecting the eyes and face from sparks, heat, and radiation.
- Welding Gloves: Protecting hands from heat and sparks.
- Welding Jacket: Providing upper body protection from heat and sparks.
- Welding Boots: Protecting feet from falling objects and sparks.
- Welding Pliers: For handling hot metal and removing slag.
- Wire Brush: For cleaning metal surfaces before and after welding.
- Chipping Hammer: For removing slag from welds.
- Angle Grinder: For preparing and finishing metal surfaces.
- Welding Table: Providing a stable and fire-resistant surface for welding.
11. Safety Measures in Welding
Safety is paramount in welding to prevent injuries and accidents.
- Personal Protective Equipment (PPE): Always wear a welding helmet, gloves, jacket, and boots.
- Ventilation: Ensure proper ventilation to avoid inhaling fumes and gases.
- Fire Safety: Keep flammable materials away from the welding area and have a fire extinguisher nearby.
- Electrical Safety: Avoid working in wet conditions and ensure equipment is properly grounded.
- Eye Protection: Always wear safety glasses or goggles when welding or grinding.
- Proper Training: Receive thorough training on equipment operation and safety procedures.
- Regular Inspections: Regularly inspect equipment for damage or wear.
12. How Long Does It Take to Learn Welding?
The time it takes to learn welding varies depending on the technique and your goals.
- Basic Welding Skills: A few weeks to a few months to learn basic techniques like MIG welding.
- Advanced Welding Techniques: Several months to years to master complex techniques like TIG welding and specialized applications.
- Professional Certification: Additional time for training and testing to obtain certifications.
- Continuous Learning: Welding is a skill that requires continuous practice and learning to stay current with new techniques and technologies.
13. Overcoming Fear and Building Confidence
Many beginners find welding intimidating, but building confidence is essential.
- Start with Simple Projects: Begin with small, manageable projects to build skills and confidence.
- Practice Regularly: Consistent practice is key to improving technique and building confidence.
- Seek Feedback: Ask experienced welders for feedback and guidance.
- Set Realistic Goals: Set achievable goals and celebrate your progress.
- Join a Welding Community: Connect with other welders for support and inspiration.
14. Advanced Techniques and Specializations
As you gain experience, you can explore advanced techniques and specializations.
- Pipe Welding: Welding pipes for high-pressure systems.
- Underwater Welding: Welding and repairing structures underwater.
- Robotic Welding: Programming and maintaining automated welding systems.
- Aerospace Welding: Welding aircraft components to stringent quality standards.
- Exotic Metals Welding: Welding materials like titanium and Inconel.
- High-Frequency Welding: Used in the creation of tube and pipe welds.
15. Resources for Continued Learning
Continuous learning is essential for staying current in the welding field.
- Welding Journals and Magazines: Providing the latest industry news and technical information.
- Online Forums and Communities: Connecting with other welders for advice and support.
- Industry Conferences and Trade Shows: Showcasing the latest technologies and products.
- Manufacturer Training Programs: Offering specialized training on specific equipment.
- Books and Manuals: Providing in-depth knowledge of welding techniques and metallurgy.
- LEARNS.EDU.VN: Offering articles, courses, and resources for welders of all skill levels.
16. The Future of Welding
Welding continues to evolve with new technologies and techniques.
- Automation: Increasing use of robotic welding systems.
- Additive Manufacturing: Using welding techniques to create 3D-printed metal parts.
- Laser Welding: Offering precise and high-speed welding.
- AI and Machine Learning: Optimizing welding processes and detecting defects.
- Sustainable Welding Practices: Reducing energy consumption and waste.
17. Success Stories of Welders
Inspiration can be found in the stories of successful welders who have excelled in their careers.
- Case Studies: Examples of welders who have built successful businesses or made significant contributions to their industries.
- Interviews: Insights from experienced welders on their career paths and advice for beginners.
- Testimonials: Stories of how welding has transformed lives and opened up new opportunities.
18. Welding as a Hobby
Welding can also be a rewarding hobby, allowing you to create custom projects and express your creativity.
- DIY Projects: Building furniture, art pieces, and custom tools.
- Metal Sculpture: Creating unique and intricate sculptures.
- Automotive Customization: Modifying and repairing vehicles.
- Home Repairs: Fixing and improving household items.
19. Finding a Welding Mentor
Having a mentor can significantly accelerate your learning and career development.
- Benefits of Mentorship: Guidance, support, and valuable insights from experienced welders.
- How to Find a Mentor: Networking at industry events, joining welding communities, and contacting local welding shops.
- Building a Mentorship Relationship: Establishing clear expectations, communicating regularly, and being open to feedback.
20. Final Thoughts: Embracing the Welding Journey
Learning to weld is a challenging but rewarding journey that requires dedication, practice, and continuous learning.
- Recap of Key Points: Understanding the challenges, mastering essential skills, and pursuing professional development.
- Encouragement for Aspiring Welders: With the right attitude and resources, anyone can become a skilled welder.
- Call to Action: Explore the resources at LEARNS.EDU.VN to start your welding journey today.
FAQ: Your Questions About Welding Answered
1. Is welding hard to learn for beginners?
Welding can be challenging for beginners due to the need for hand-eye coordination, understanding safety protocols, and familiarizing oneself with equipment. However, with proper training and practice, it is manageable. MIG welding is often considered the easiest to start with.
2. What are the easiest welding techniques to learn?
MIG (GMAW) and stick (SMAW) welding are generally considered the easiest techniques for beginners. MIG welding is often compared to using a glue gun due to its simplicity, while stick welding is versatile and doesn’t require a shielding gas.
3. How long does it take to become proficient in welding?
Proficiency in welding can take anywhere from a few months to several years, depending on the level of skill you want to achieve. Basic skills can be acquired in a few weeks, while mastering advanced techniques may take years of practice.
4. Do I need formal education to become a welder?
While formal education isn’t always mandatory, it is highly recommended. Vocational schools, community colleges, and apprenticeship programs offer comprehensive training that can significantly enhance your skills and career prospects.
5. What are the essential safety measures in welding?
Essential safety measures include wearing personal protective equipment (PPE) such as a welding helmet, gloves, and jacket, ensuring proper ventilation, keeping flammable materials away from the welding area, and having a fire extinguisher nearby.
6. What career opportunities are available for welders?
Welders can pursue various career paths, including structural welding, pipe welding, automotive welding, aerospace welding, underwater welding, robotic welding, welding inspection, welding engineering, and welding instruction.
7. How much can I earn as a welder?
The earning potential for welders varies depending on experience, location, and specialization. Experienced welders can earn competitive salaries, and those with specialized skills like underwater welding can earn significantly more.
8. What is the American Welding Society (AWS)?
The American Welding Society (AWS) is a non-profit organization that sets standards for welding and offers certifications for various welding processes and specialties. It’s a valuable resource for welders looking to enhance their skills and career prospects.
9. Can I learn welding online?
Yes, you can learn welding basics online through videos and tutorials. However, hands-on practice and in-person instruction are crucial for developing proficiency. Online resources can supplement formal training but should not replace it entirely.
10. What tools and equipment do I need to start welding?
Essential tools and equipment include a welding machine, welding helmet, welding gloves, welding jacket, welding boots, welding pliers, wire brush, chipping hammer, angle grinder, and a welding table.
Embarking on a welding journey can be both challenging and incredibly rewarding. Whether you’re looking to master a new skill for a career or explore a creative hobby, understanding the fundamentals, committing to safety, and continuously learning are key. At LEARNS.EDU.VN, we’re dedicated to providing you with the resources and guidance you need to succeed. From detailed articles and tutorials to expert advice, we’re here to support you every step of the way.
Ready to take the next step? Visit LEARNS.EDU.VN today to explore our welding courses and resources. Located at 123 Education Way, Learnville, CA 90210, United States, we’re here to help you achieve your welding goals. Contact us via WhatsApp at +1 555-555-1212 for more information. Start your journey with learns.edu.vn and discover the endless possibilities that welding can offer.